Smart Solutions: How Pokayoke Systems are Revolutionizing Automotive Manufacturing
"Discover how Programmable Logic Controllers (PLCs) enhance precision and safety in actuator bracket assembly, reducing defects and improving quality in automotive production."
In the fast-paced world of automotive manufacturing, precision and quality are paramount. Every component, no matter how small, plays a crucial role in the overall performance and safety of a vehicle. One critical area is the mounting of actuator brackets, where even minor errors can lead to significant quality and safety issues. Traditional manual processes, while reliable to a degree, are prone to human error, which can result in defects and costly rework.
To combat these challenges, automotive manufacturers are increasingly turning to innovative error-proofing techniques known as Pokayoke systems. These systems, often integrated with Programmable Logic Controllers (PLCs), are designed to prevent mistakes before they occur, ensuring that each component is assembled correctly and consistently. By automating error detection and correction, Pokayoke systems not only improve product quality but also enhance efficiency and reduce waste.
This article delves into the design and implementation of Pokayoke systems in the context of actuator bracket assembly. We'll explore how PLCs are used to create intelligent systems that guide operators, detect errors in real-time, and ensure that every bracket is mounted to the highest standards. Join us as we uncover how these smart solutions are revolutionizing automotive manufacturing, one bracket at a time.
The Challenge of Actuator Bracket Assembly
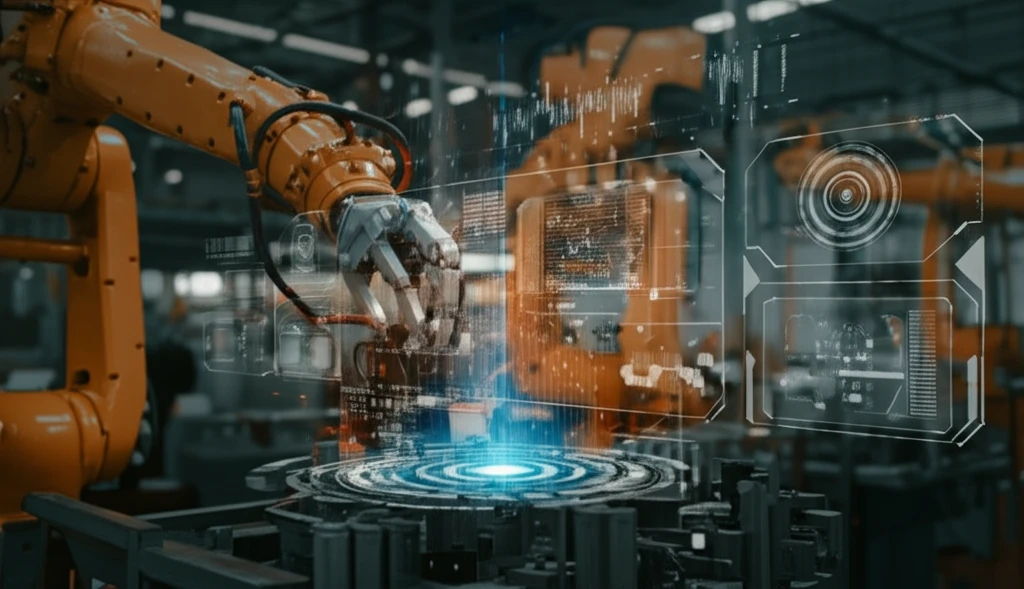
Actuator brackets are essential components in a vehicle's braking system. These brackets must be mounted with utmost precision, typically using three bolts per side, each tightened to a specific torque value (e.g., 5.4 Nm). Manual assembly, while seemingly straightforward, can be fraught with errors. Operators might inadvertently miss a bolt, under-tighten or over-tighten it, or even use the wrong type of bolt. Such errors can compromise the integrity of the braking system, leading to potential safety hazards.
- Error Prevention: Pokayoke systems are designed to prevent errors from occurring in the first place, rather than simply detecting them afterward.
- Automated Checks: These systems incorporate sensors and PLCs to automatically verify that each step in the assembly process is performed correctly.
- Real-Time Feedback: Operators receive immediate feedback on their actions, guiding them through the correct sequence and torque settings.
- Line Stop: If an error is detected, the system can halt the production line, preventing further defective units from being produced.
Future Directions and Innovations
The design of the Pokayoke system on the mounting of the actuator bracket is to improve the process of mounting the actuator bracket. In this case it is to prevent errors in the torque process on one of the bolts with a standard torque of 5.4 Nm. This pokayoke system design prevents the occurrence of damaged bolts on screw threads when mounting an imperfect actuator bracket. The design of this pokayoke system can also eliminate the process of repair caused by poor installation and require additional cost for the repair process. This Pokayoke system is still a potential for miss tightening, then it takes a tool that can detect the position of bolts that have been processed by using the nut runner.