Revolutionizing Manufacturing: How Dry Deep Drawing is Changing the Game
"Discover how volatile media is transforming deep drawing, making it cleaner, more efficient, and sustainable. Learn about the groundbreaking research and practical applications that are setting a new standard in metal forming."
In today's manufacturing world, sustainability and the elimination of harmful substances are more than just buzzwords—they're critical drivers of innovation. Traditional deep drawing, a cornerstone of metal forming, often relies on mineral lubricants to reduce friction and prevent surface damage. However, these lubricants come with their own set of problems, including the presence of harmful additives like chlorinated paraffins.
These substances not only pose environmental and health risks but also require additional steps in the manufacturing process. Lubricants must be applied before forming and then meticulously removed to avoid interfering with subsequent processes like bonding, welding, and painting. It's a costly and time-consuming cycle that manufacturers are eager to escape.
Enter the groundbreaking technique of dry deep drawing, which replaces traditional lubricants with volatile media such as nitrogen or carbon dioxide. This innovative approach promises to eliminate harmful substances, streamline production, and significantly enhance the sustainability of manufacturing processes.
The Science Behind Dry Deep Drawing
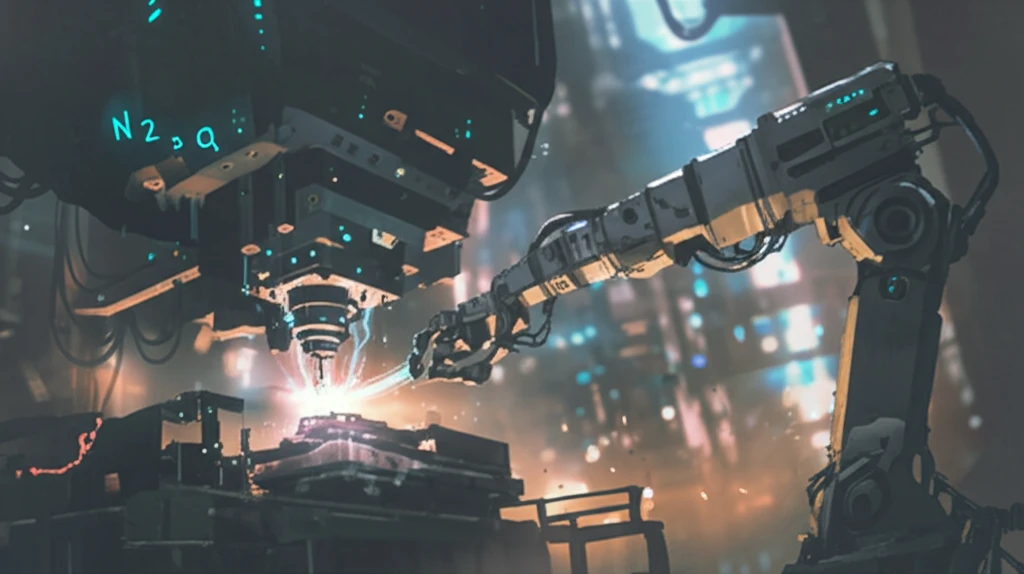
The core principle of dry deep drawing involves introducing volatile media directly into the tools during the forming process. This creates a lubricating layer between the tool and the sheet metal, reducing friction and preventing wear. The real magic happens after the forming is complete: the volatile media evaporates without leaving any residue, eliminating the need for post-processing cleaning.
- Flat Strip Drawing Tests: These tests help determine the achievable coefficients of friction using different volatile media and varying parameters like media pressure and the geometry of laser-drilled microholes.
- Strip Drawing Tests with Deflection: This method examines friction conditions at tool radii, simulating the bending and pressure experienced in real-world deep drawing scenarios.
- Deep-Drawing Tests of Rectangular Cups: These tests assess the feasibility and stability of the process, comparing it to conventional lubrication methods.
The Future of Manufacturing is Here
The transition to dry deep drawing isn't just about adopting a new technique—it's about embracing a new philosophy of manufacturing. By eliminating harmful substances, streamlining processes, and enhancing sustainability, dry deep drawing offers a pathway to a cleaner, more efficient, and more responsible future. As research continues and these methods are refined, we can expect to see even wider adoption of this transformative technology across various industries.