Rethinking Composite Materials: How New Vibration Analysis Can Revolutionize Design
"Discover how a novel approach to analyzing vibrations in laminated composite plates could lead to safer, lighter, and more efficient designs in everything from aircraft to sporting equipment."
Composite materials, known for their strength and lightness, are everywhere—from the sleek wings of modern aircraft to the high-performance frames of bicycles. But harnessing their full potential requires precise understanding of how they behave under stress, especially when vibrating. Traditional methods often fall short, leading to designs that are either over-engineered or, worse, prone to failure.
Now, a cutting-edge approach is changing the game. The 'Sampling Surfaces' (SaS) method offers a more detailed and accurate way to analyze vibrations in laminated composite plates. This innovation promises not only to refine existing applications but also to unlock new possibilities for these versatile materials.
Imagine lighter, more fuel-efficient vehicles, safer aircraft, and even more responsive sports equipment—all made possible by a deeper understanding of how these materials respond to vibration. This is the promise of the SaS method, a tool that empowers engineers to push the boundaries of design and performance.
What is the Sampling Surfaces (SaS) Method and Why Is It a Big Deal?
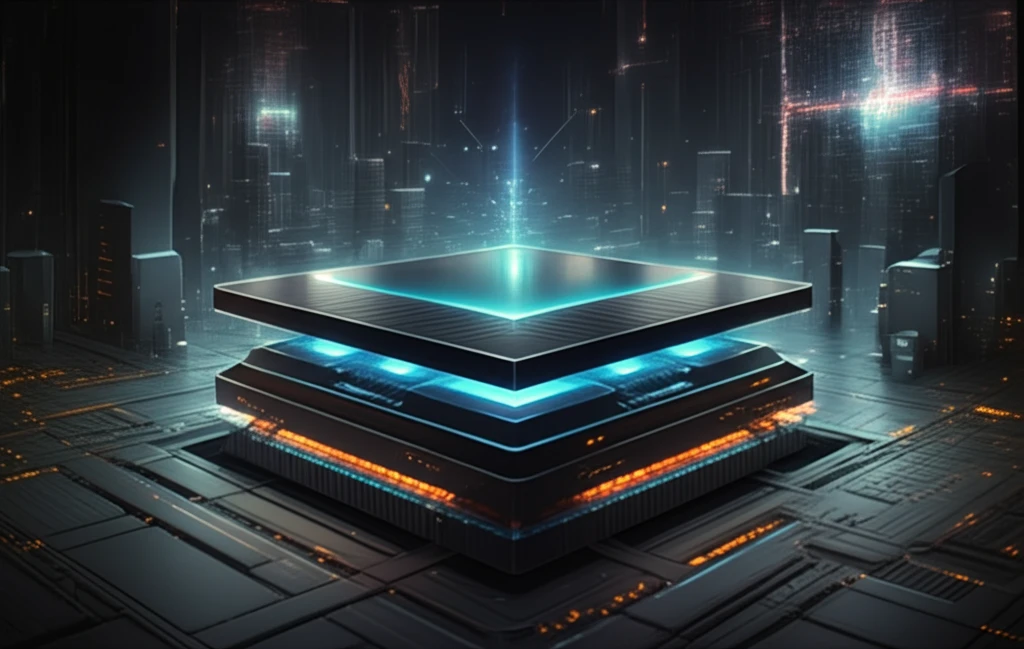
At its core, the SaS method is a sophisticated technique for analyzing the stresses and vibrations within composite materials. Unlike traditional methods that approximate these complex behaviors, SaS uses a network of 'sampling surfaces' strategically placed within the material to capture a highly detailed picture of its internal dynamics.
- Greater Accuracy: Provides a more precise understanding of vibration behavior compared to traditional methods.
- Design Optimization: Enables engineers to fine-tune designs for optimal strength, weight, and performance.
- Material Efficiency: Reduces material waste by identifying areas where less material can be used without compromising structural integrity.
- Enhanced Safety: Helps prevent failures by identifying potential weak points and ensuring designs can withstand real-world stresses.
- Versatility: Can be applied to a wide range of composite structures, from aerospace components to automotive parts.
The Future of Composite Design is Here
The Sampling Surfaces method represents a significant leap forward in our ability to understand and utilize composite materials. As industries continue to demand lighter, stronger, and more efficient structures, this technology will undoubtedly play a crucial role in shaping the future of design and engineering. From the cars we drive to the planes we fly, SaS promises to unlock the full potential of these remarkable materials, leading to safer, more sustainable, and higher-performing products.