Precision Perfected: How Iterative Learning Control is Revolutionizing CNC Milling
"Unlock enhanced accuracy and efficiency in your CNC milling processes with segmented iterative learning control. Discover how this innovative method minimizes volumetric errors for superior part programs."
In manufacturing, the relentless pursuit of higher accuracy has driven innovation in Computerized Numerical Control (CNC) machine tools. As conventional methods struggle to meet increasingly stringent requirements, manufacturers are turning to advanced techniques to enhance precision and minimize errors. One such technique is the application of Iterative Learning Control (ILC) to volumetric error compensation.
Volumetric error, a culmination of various geometric inaccuracies within a machine tool's working volume, significantly impacts the accuracy of finished parts. Traditionally, addressing volumetric error has been complex and costly, often involving expensive machine tool controllers. However, recent advances in software-based compensation methods offer a more accessible and adaptable solution.
This article delves into the groundbreaking approach of Segmented Iterative Learning Control (ILC) for CNC milling, a method that refines tool paths, compensates for volumetric errors, and ultimately achieves unprecedented precision in manufacturing. We'll explore the principles behind this technique, its implementation, and the potential benefits it offers for manufacturers striving for excellence.
Understanding Volumetric Error and the Need for Compensation
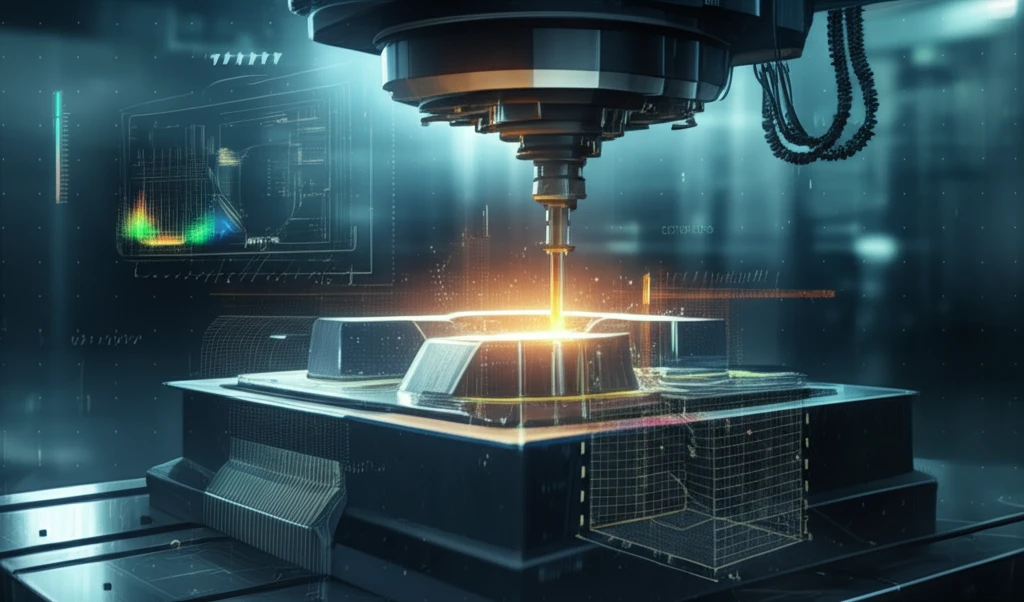
Volumetric error in CNC milling arises from the accumulation of 21 static geometric errors within the machine. These errors encompass displacement errors (linear, vertical, and horizontal straightness) and angular errors (pitch, yaw, and roll). The cumulative effect of these inaccuracies leads to deviations in the tool's actual position compared to its intended path, ultimately affecting the dimensional accuracy of the workpiece.
- Enhanced Accuracy: Achieve tighter tolerances and reduce deviations in finished parts.
- Improved Surface Finish: Minimize tool path inaccuracies that lead to imperfections.
- Reduced Scrap and Rework: Prevent errors before they occur, saving time and material.
- Increased Efficiency: Optimize tool paths for faster and more precise milling operations.
- Cost Savings: Avoid the need for expensive machine tool upgrades or specialized controllers.
The Future of Precision Milling
The segmented iterative learning control method represents a significant advancement in CNC milling technology. By addressing the limitations of traditional error compensation techniques, this approach empowers manufacturers to achieve unprecedented levels of precision, efficiency, and quality in their machining operations. As the demand for high-precision components continues to grow across industries, methods like segmented ILC will play an increasingly vital role in shaping the future of manufacturing.