Popping Under Pressure: How Tiny Bubbles Could Revolutionize High-Temperature Materials
"Scientists uncover the secrets of bubble formation in advanced ceramics, paving the way for stronger, more durable materials for extreme environments. Learn about ZrB2 composites and their potential."
Imagine a world where materials can withstand the most extreme conditions—scorching heat, intense pressure, and corrosive environments. This is the promise of ultra-high temperature ceramics (UHTCs), a class of materials designed to push the boundaries of engineering. Among these, Zirconium Diboride (ZrB2) composites stand out for their exceptional melting points and chemical stability, making them ideal for aerospace, defense, and energy applications. However, a tiny but mighty foe threatens their performance: bubbles.
When ZrB2 composites are exposed to high temperatures, a phenomenon known as 'bubble formation' occurs. This involves the creation and subsequent rupture of gas-filled cavities within the material's structure. While seemingly insignificant, these bubbles can drastically compromise the material's integrity, leading to oxidation and ablation—essentially, the material's slow but sure destruction. Understanding the intricacies of this process is crucial for unlocking the full potential of ZrB2 composites.
New research is shedding light on how these bubbles form, grow, and eventually burst. By manipulating the material’s composition and microstructure, scientists aim to mitigate the detrimental effects of bubble formation, paving the way for more robust and reliable high-temperature materials.
The Science of Bubbles: Unraveling the Formation Mechanism
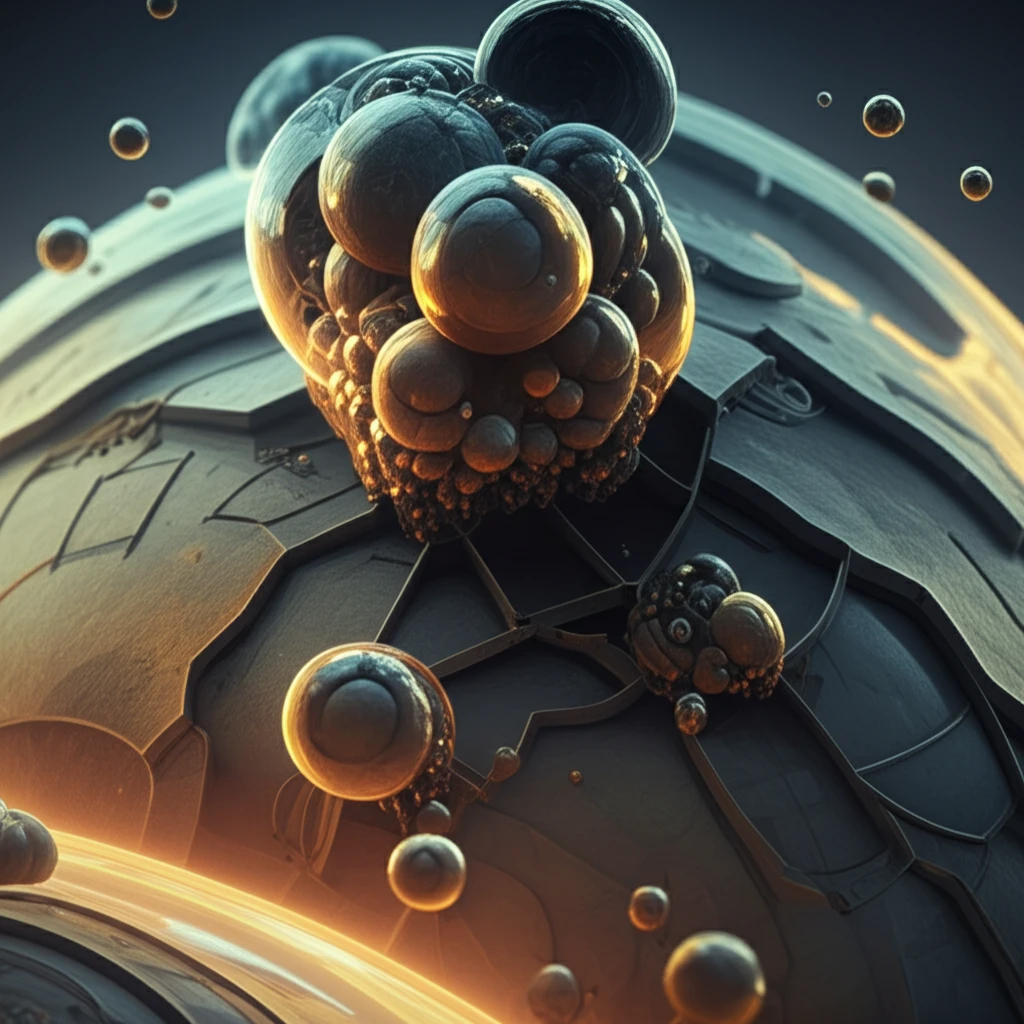
At high temperatures, ZrB2 composites undergo oxidation, leading to the formation of various gaseous products, including silicon dioxide (SiO2) and boron oxide (B2O3). These gases can become trapped within the material, forming bubbles. The process isn't random; it's governed by a complex interplay of factors, including temperature, pressure, and the material's microstructure. Recent studies have focused on understanding the step-by-step mechanism of bubble formation, from the initial nucleation to the final rupture.
- Gas Composition: The type and amount of gases produced during oxidation directly impact bubble formation.
- Temperature: Higher temperatures accelerate oxidation and gas production, increasing the likelihood of bubble formation.
- Material Microstructure: The arrangement of grains and phases within the composite affects gas diffusion and bubble migration.
- Viscosity: The viscosity of the liquid oxide layers influences bubble movement and rupture.
Engineering Solutions: Preventing the Pop
The ongoing research offers promising avenues for improving the performance of ZrB2 composites. Strategies include modifying the material's composition to reduce the formation of detrimental gases, engineering the microstructure to enhance gas diffusion, and introducing additives to strengthen the oxide layers. One promising approach is to replace some of the ZrB2 with carbides, such as Zirconium Carbide (ZrC), as this reduces the production of B2O3. The CO and CO2 gases produced by ZrC oxidation are smaller and escape more easily, preventing large bubble formation.