Navigating the Future: How Advanced Control Systems are Revolutionizing MEMS Gyroscopes
"Unlocking Precision: Exploring Sliding Mode Control and Robust Design in Micro-Electro-Mechanical Systems"
In an era defined by automation and precision, angular velocity sensors, commonly known as gyroscopes, play a pivotal role. From stabilizing drones to guiding spacecraft, these devices estimate angular velocity across diverse applications. While traditional gyroscopes like spinning discs and fiber optic models have served us well, the rise of Micro-Electro-Mechanical Systems (MEMS) gyroscopes has marked a significant leap forward.
MEMS gyroscopes offer a compelling combination of low power consumption, energy efficiency, compact size, and cost-effectiveness. These qualities have fueled their proliferation in everything from smartphones and toys to sophisticated weaponry and automobiles. As Inertial Measurement Units (IMUs) continue to evolve, MEMS technology is increasingly vital for both industrial and tactical-grade sensing applications.
Despite their advantages, MEMS gyroscopes face technical and commercial hurdles. Manufacturing variations, parameter uncertainties, and external disturbances like electrical and thermal noise can significantly degrade their performance, causing deviations from specifications and potential failures. These imperfections can lead to discrepancies between expected and actual performance, necessitating advanced control mechanisms to mitigate these 'parasitic' effects.
Why is Robust Control Crucial for MEMS Gyroscopes?
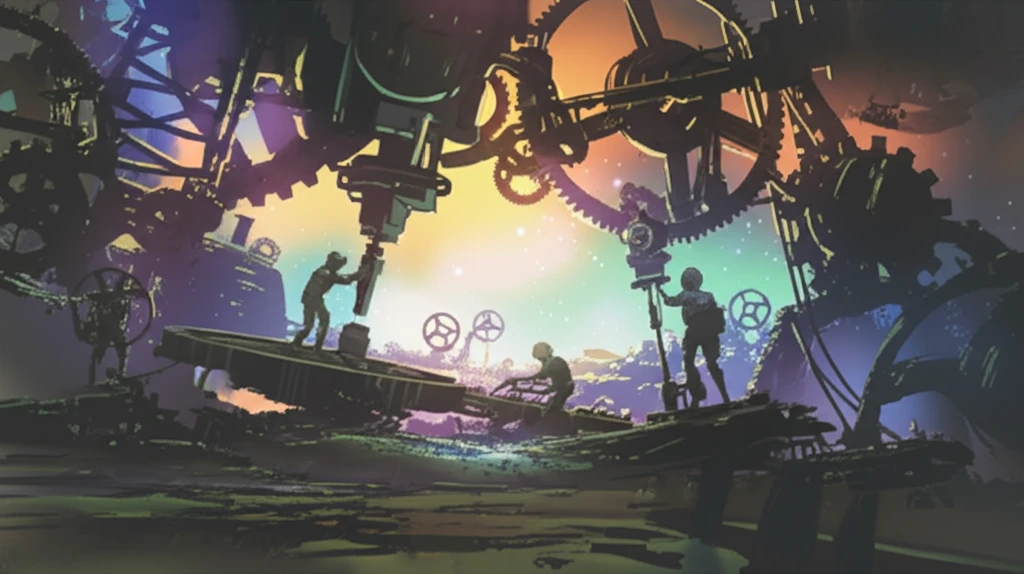
Ideally, MEMS gyroscope modes should operate independently with perfectly matched natural frequencies, ensuring that the output is solely dependent on the angular rate. However, real-world fabrication flaws and environmental distortions introduce frequency disparities and unwanted coupling, leading to erroneous outputs. To counteract these issues, robust control systems are essential.
- Neglecting mechanical coupling caused by manufacturing imperfections.
- Ignoring noise considerations in adaptive controllers.
- Failing to account for the substantial movement of the proof mass along the drive axis in adaptive modes.
- Overlooking driving mode control while regulating sense mode oscillation.
The Future of MEMS Gyroscope Control
The development and implementation of advanced control strategies like sliding mode control represent a significant step forward in enhancing the reliability and precision of MEMS gyroscopes. By addressing the inherent imperfections and external disturbances that affect these devices, we can unlock their full potential across a wide range of applications. As technology evolves, continued innovation in control system design will be crucial for maintaining the performance and accuracy of MEMS gyroscopes in an increasingly demanding world.