Laser Cutting: Which Metal Matrix Composite Reigns Supreme?
"A Deep Dive into Machining Characteristics of Composites Using CO2 Laser Technology"
Metal matrix composites (MMCs) are revolutionizing industries due to their exceptional properties. These advanced materials, tailored for specific applications, combine a metal with ceramic reinforcement, unlocking unique performance capabilities. However, their complex composition presents machining challenges, particularly with traditional methods.
Laser beam machining (LBM) emerges as a powerful solution, offering speed, precision, and excellent surface finish. While LBM excels at cutting various materials, its performance with MMCs is influenced by the type, size, and distribution of reinforced particles. This article delves into the machining characteristics of MMCs using CO2 laser cutting, comparing the effects of different reinforcing particles like SiC, Al2O3, and ZrO2.
We will explore how factors like cutting speed, particle type, and cut profile impact the final quality of the machined MMCs. The investigation includes analysis of dross height, kerf deviation, and striation angle, along with microstructural examinations to understand particle behavior during the laser cutting process.
Understanding the Laser Cutting Process and Variables
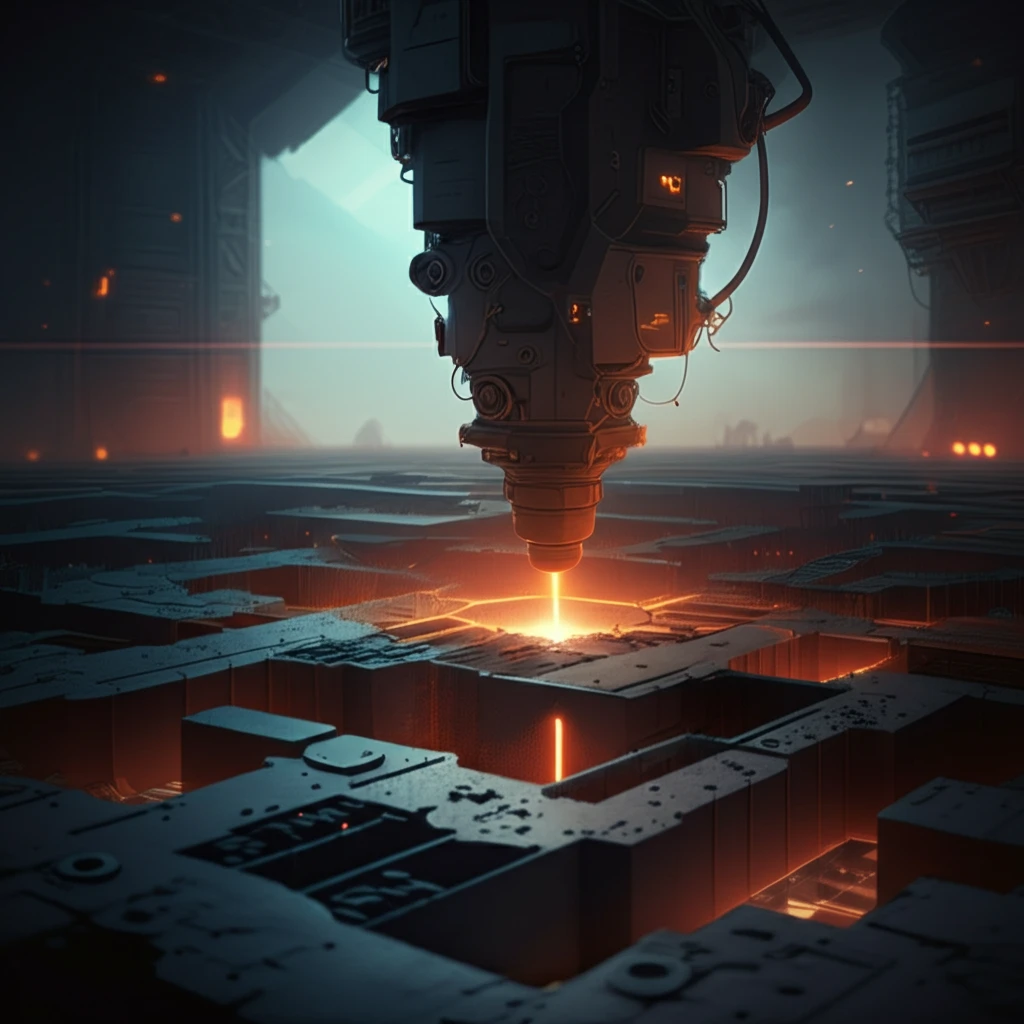
The study systematically explores the effects of laser cutting parameters on MMC materials reinforced with silicon carbide (SiC), aluminum oxide (Al2O3), and zirconium oxide (ZrO2). It investigates how different parameters affect the characteristics of the cut, such as the height of the dross, the kerf deviation, and the angle of striations.
- Cutting Speed: The rate at which the laser moves across the material, influencing heat input and material removal efficiency.
- Laser Power: Affects the amount of energy delivered to the material, crucial for melting and vaporizing the composite.
- Standoff Distance: The distance between the laser nozzle and the material surface, impacting focus and energy density.
- Nozzle Diameter: Controls the flow and concentration of assist gas, which helps remove molten material.
- Gas Pressure: Affects the removal of molten material and cooling rate of the cut edge.
- Reinforced Particles: The type and percentage of ceramic particles (SiC, Al2O3, ZrO2) within the metal matrix, influencing machinability.
- Arc Radius: For curved cuts, the radius of the arc affects the consistency of the laser's interaction with the material.
Implications and Future Directions
This research provides critical insights into the laser machining of metal matrix composites, highlighting the importance of parameter selection and material composition. By understanding how different reinforcing particles and laser settings interact, manufacturers can optimize their processes to achieve superior cut quality and material performance. Further research could explore advanced laser techniques and novel composite materials to push the boundaries of precision manufacturing.