Knitted Composites: The Surprising Science Boosting Everyday Materials
"Learn how cutting-edge research is using knitted fabrics to revolutionize the strength and sustainability of single polymer composites."
In the world of materials science, the quest for stronger, lighter, and more sustainable materials is constant. Traditional composite materials, which combine different substances, have long been a staple in industries ranging from aerospace to construction. However, a new frontier has emerged: single polymer composites (SPCs). These innovative materials use a matrix and reinforcement made of the same polymer, offering unique advantages in terms of recyclability and bonding.
Recent research has taken SPCs a step further by incorporating knitted textile structures. This approach leverages the inherent flexibility and strength of knitted fabrics to create composites with enhanced mechanical properties. The focus is on using polyamide 6 (PA6), a versatile and widely used polymer, as both the matrix and the reinforcing element. By carefully controlling the manufacturing process, scientists are creating materials that outperform traditional composites in specific applications.
This article delves into the fascinating world of knitted-reinforced SPCs, exploring the innovative techniques used to create them and the potential impact on various industries. We'll break down the science in an accessible way, revealing how these advanced materials are poised to transform the future of manufacturing.
The Magic of Knitted Reinforcements
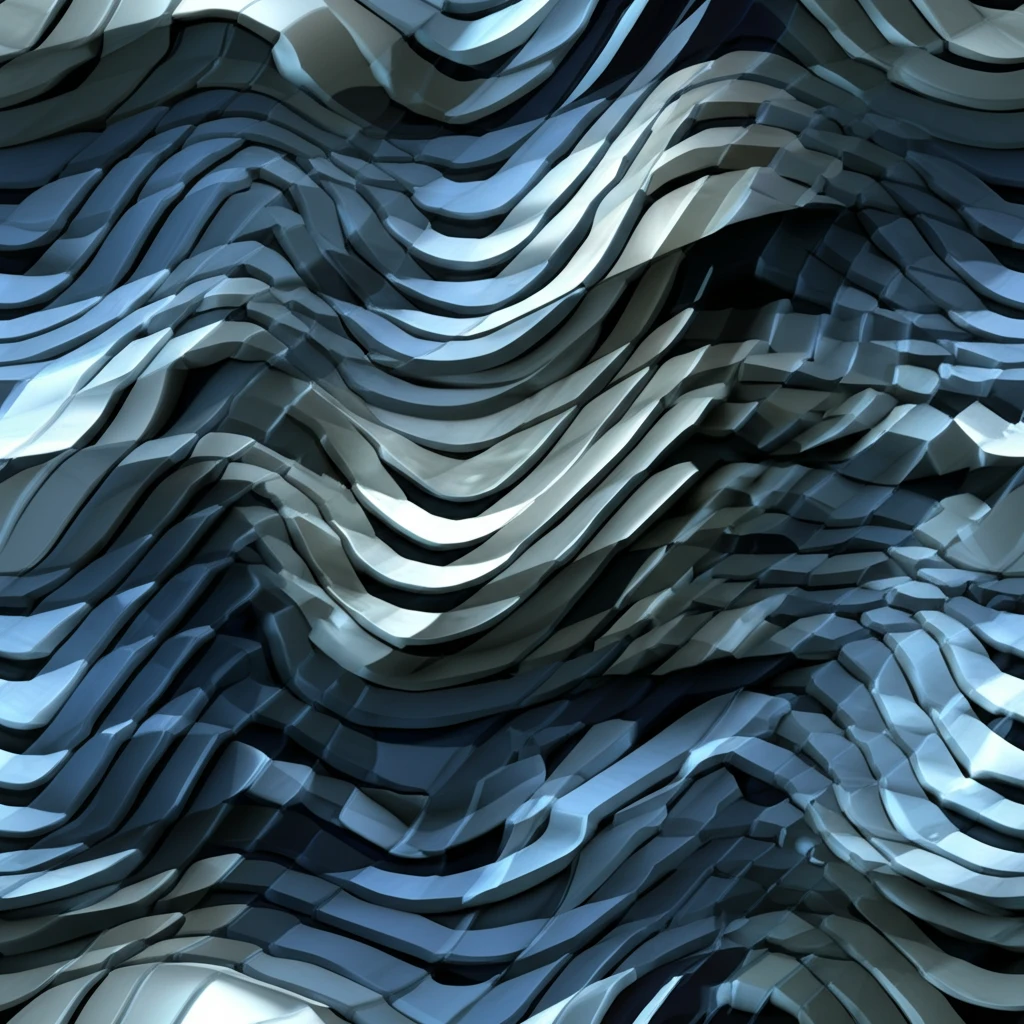
The core of this innovation lies in the unique properties of knitted fabrics. Unlike woven materials, knitted structures offer greater flexibility and conformability, allowing them to be easily integrated into complex shapes. When used as reinforcement in SPCs, these knitted fabrics provide exceptional strength and resistance to tearing. The specific type of knit pattern also plays a crucial role. Researchers are experimenting with different knit structures, such as Jersey and Rib 1x1, to optimize the composite's performance for specific applications.
- NYRIM: Precise control over matrix formation.
- PCCM: Utilizes pre-made PA6 powders for composite creation.
- Knit Structure: Jersey and Rib 1x1 patterns offer different strengths.
- Volume Fraction: Balancing reinforcement for optimal composite characteristics.
The Future of Materials
The development of knitted-reinforced SPCs represents a significant step forward in materials science. These innovative materials offer a unique combination of strength, flexibility, and sustainability, making them ideal for a wide range of applications. As researchers continue to refine the manufacturing process and explore new knit patterns and polymer combinations, we can expect to see these advanced composites playing an increasingly important role in shaping the future of manufacturing.