How Does Wear Affect High-Precision Machinery? A Guide to Hybrid Conical Journal Bearings
"Explore the impact of wear on hybrid conical journal bearings and learn how engineers are innovating to maintain performance and longevity in critical machinery."
In the world of engineering, precision is paramount. High-performance machinery relies on components that can withstand immense stress while maintaining accuracy. One such component is the hybrid conical journal bearing, a sophisticated piece of equipment designed for exceptional performance. These bearings are used in applications where both radial and axial loads need to be supported simultaneously, making them ideal for demanding industrial settings.
However, even the most meticulously designed components are susceptible to wear. Over time, the continuous operation and harsh conditions can degrade the surfaces of these bearings, impacting their efficiency and reliability. Understanding how wear affects these bearings is crucial for engineers to optimize designs and predict maintenance needs.
This article explores the findings of recent research on the effects of wear on hybrid conical journal bearings. It will delve into how wear alters the performance characteristics of these bearings and what steps can be taken to mitigate these effects, ensuring the longevity and reliability of high-precision machinery.
Understanding the Impact of Wear on Bearing Performance
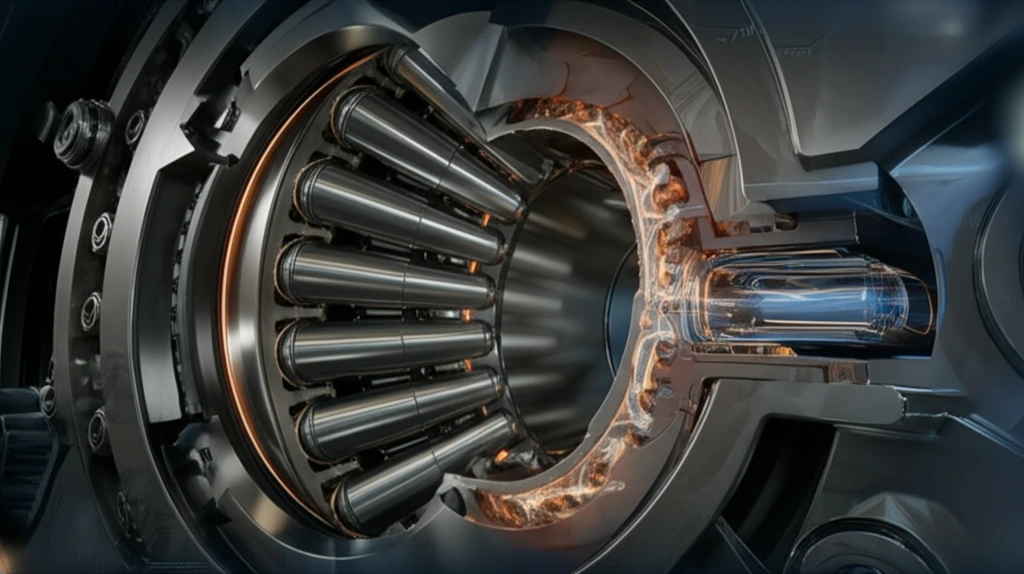
Hybrid conical journal bearings combine hydrostatic and hydrodynamic actions to support both radial and axial loads. The hydrostatic action uses pressurized fluid to maintain a gap between the moving surfaces, reducing friction, while the hydrodynamic action generates a fluid film due to the bearing's motion. This combination provides excellent stiffness at various speeds and a high load capacity.
- Frequent start and stop operations: These cause rubbing between surfaces before the fluid film is fully established.
- Heavy loads: High loads increase the stress on bearing surfaces, accelerating wear.
- Contamination: Abrasive particles in the lubricant can cause significant wear.
- Material properties: The hardness and wear resistance of the bearing materials play a crucial role.
Looking Ahead: Innovations in Bearing Design
The research highlights the critical need to account for wear in the design and maintenance of hybrid conical journal bearings. By understanding how wear affects performance, engineers can develop strategies to extend bearing life and improve machinery reliability. This includes exploring advanced materials, optimizing lubrication systems, and implementing predictive maintenance techniques.