Hidden Dangers: Unmasking Corrosion in Plate Heat Exchangers
"Comprehensive analysis reveals how pitting, crevice corrosion, and fretting cooperate to cause internal leakage in plate heat exchangers, threatening industrial safety and efficiency."
Plate heat exchangers (PHEs) are indispensable in various industries because of their compact design, ease of maintenance, and high efficiency. From dairy and food processing to chemical industries, co-generation power plants, and central cooling systems, PHEs play a vital role in thermal management. However, the corrugated austenitic stainless steel (ASS) plates, the heart of PHEs, face relentless degradation due to harsh environmental conditions.
In China, heating power plants using PHEs are increasingly experiencing internal leakage, jeopardizing both plant safety and operational efficiency. Studies indicate that local corrosion, leading to cracking and perforation, is a primary cause of these leaks. Traditional assumptions pointed to stress corrosion cracking (SCC) in 304-type ASS plates, triggered by cold working-induced stress and chloride ion build-up. Others highlighted pitting corrosion from high chloride content. However, these explanations often fell short of fully explaining the observed failures.
This article explores a comprehensive failure analysis of 316L plates from a co-generation power plant, revealing a complex interplay of factors beyond simple corrosion. By investigating design flaws, manufacturing quality, and operational conditions, we aim to provide insights into preventing PHE failures and ensuring reliable performance.
The Cooperative Corrosion Culprits: Pitting, Crevice Corrosion, and Fretting
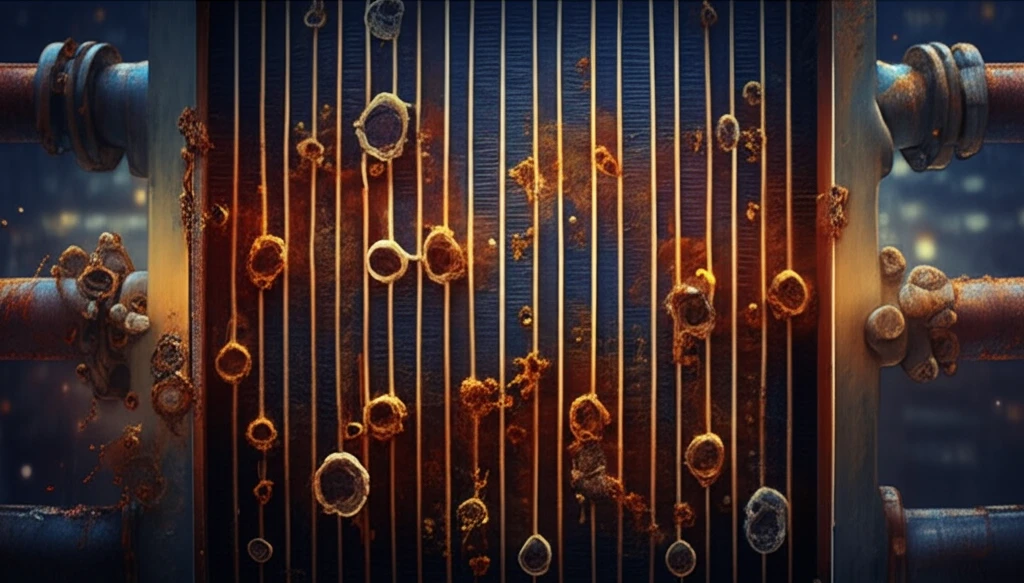
The investigation focused on bowl-like perforations regularly distributed at crossing contact points (CCPs) between the corrugated plates. While initial assessments leaned towards typical failure mechanisms, the unique characteristics of these perforations prompted a deeper analysis. It was determined that these perforations resulted from the cooperation of pitting, crevice corrosion, and fretting.
- Pitting: Localized corrosion that creates small holes.
- Crevice Corrosion: Occurs in gaps where stagnant solution can lead to concentrated corrosion.
- Fretting Corrosion: Corrosion damage accelerated by repetitive surface contact and pressure.
- Synergistic Effect: Cooperation of pitting, crevice corrosion, and fretting makes corrosion occur.
Preventing Future Failures: Practical Recommendations
Based on the analysis, several measures can be implemented to mitigate the risk of PHE failures: Strict control of chloride levels in the LTHW, maintaining consistent pressure between HTHW and LTHW to minimize fretting, and implementing regular repassivation treatments. By addressing design vulnerabilities, manufacturing quality, and operational conditions, industries can significantly extend the lifespan and reliability of their plate heat exchangers, ensuring safer and more efficient operations.