Gear Up for Efficiency: How Asymmetric Design Optimizes Micropump Performance
"Uncover the secrets of gear micropump asymmetry and its impact on stress distribution, leading to enhanced durability and performance in hydraulic systems."
Gear pumps are the unsung heroes of hydraulic systems, powering everything from heavy machinery to essential ship components. Within this category, micropumps stand out for their compact size and crucial role in precision applications, especially in harsh environments like the marine sector. These tiny powerhouses face immense pressure and stress, making their structural integrity paramount.
Traditional symmetrical designs have been the standard, but recent research suggests that introducing asymmetry can lead to significant performance enhancements. By strategically shifting internal components, engineers can redistribute stress, potentially extending the lifespan and reliability of these critical devices. This concept challenges conventional wisdom and opens new avenues for optimizing micropump design.
This article dives into the groundbreaking findings of a study that explores the impact of asymmetric design on gear micropump body stress distribution. We'll unpack the numerical calculations, explore the optimal positioning of key components, and reveal how these subtle shifts can lead to remarkable improvements in performance and durability. Whether you're an engineer, a marine industry professional, or simply curious about the world of hydraulics, prepare to discover the power of asymmetry.
The quest for balance: How asymmetry changes the game for stress management in micropumps?
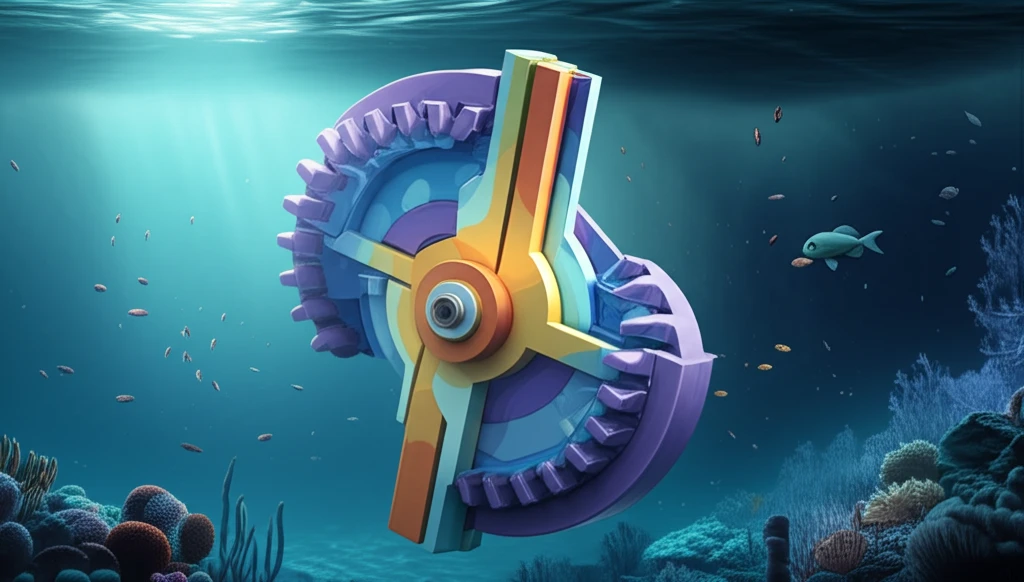
The core of the investigation lies in understanding how shifting the location of bushings and the pumping unit within the gear pump body affects stress distribution. Researchers analyzed fourteen different configurations, ranging from perfectly symmetrical to those with components shifted by up to 2.6 mm towards the suction channel. Think of it like fine-tuning a complex instrument – small adjustments can produce significant changes in the overall sound.
- Reduced Maximum Stress: The peak stress within the pump body dropped to 109 MPa, a significant decrease compared to the symmetrical design.
- Minimized Displacement: The highest displacement, a measure of deformation under stress, was only about 15µm.
- Satisfied Strength and Stiffness: The modified pump body met all required strength and stiffness criteria, ensuring its ability to withstand the rigors of operation.
The future of micropumps: Embracing asymmetry for enhanced performance
The study's findings pave the way for a new generation of micropumps that leverage asymmetric design to achieve superior performance and durability. While the 2.2 mm shift proved optimal in this particular case, the underlying principle can be applied to other pump designs and operating conditions. This opens up exciting possibilities for tailoring micropumps to specific applications and maximizing their efficiency.