Future-Proof Your Factory: How Real-Time Predictive Maintenance Cuts Downtime and Boosts Profits
"Discover the power of complex event processing (CEP) and how it's revolutionizing manufacturing by predicting equipment failures before they happen."
In today's fast-paced industrial landscape, where efficiency and reliability are paramount, the ability to predict and prevent equipment failures before they occur is no longer a luxury but a necessity. The convergence of advanced computing technologies and innovative information and communication systems has paved the way for a transformative approach to maintenance: real-time predictive maintenance.
Real-time predictive maintenance is about rapidly identifying and categorizing potential issues and their locations, allowing for swift intervention and minimizing disruptions. Central to this approach is complex event processing (CEP), a concept that enables constant surveillance of a system's condition, identifies the root causes of faults, and evaluates the health of technical components, all in real-time.
Think of it as a vigilant guardian watching over your factory floor, instantly spotting anomalies and alerting you to potential problems before they escalate into full-blown crises. This proactive approach not only minimizes downtime but also optimizes resource allocation, ensuring that maintenance efforts are focused where they are most needed.
The Power of Prediction: How CEP Works
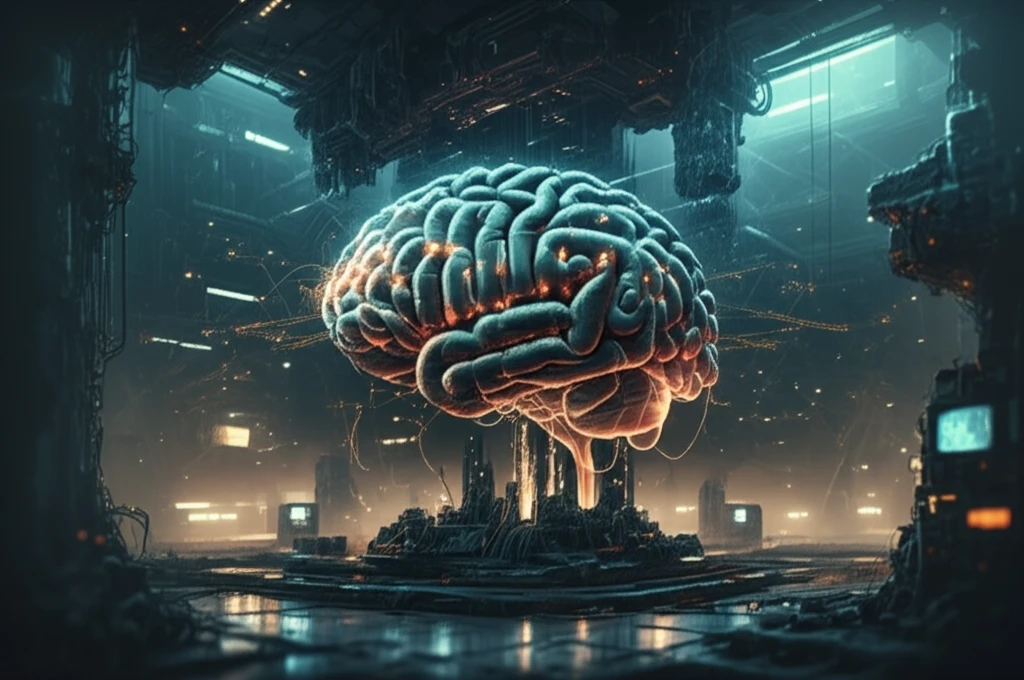
Traditionally, maintenance management was viewed as a cost center. Now it's a strategic function deeply integrated into the value creation process. In a global market defined by intense competition, manufacturers need machines and plants that operate with unwavering reliability to avoid costly downtime and stay ahead.
- Real-Time Insights: CEP facilitates continuous monitoring of system states, providing instant alerts upon detection of anomalies.
- Root Cause Analysis: The technology swiftly identifies the underlying causes of potential failures, enabling targeted interventions.
- Optimized Maintenance: By evaluating component health, CEP ensures maintenance efforts are directed where they yield the highest impact.
- Strategic Planning: The insights gained from CEP inform maintenance schedules and resource allocation, maximizing efficiency.
Embrace the Future of Maintenance
The journey towards real-time predictive maintenance with CEP is an ongoing process of refinement and adaptation. As technology evolves and new data sources become available, the models and algorithms that drive CEP systems will need to be continuously updated and improved. By embracing this proactive approach, businesses can unlock new levels of efficiency, reliability, and profitability, ensuring they remain competitive in an increasingly dynamic and demanding marketplace. Are you ready to transform your maintenance strategy and future-proof your operations?