Fuel Cell Breakthrough: How Cobalt Could Revolutionize Clean Energy
"New research explores the impact of cobalt oxide on LSCF-based cathodes, paving the way for more efficient and cost-effective solid oxide fuel cells."
In a world increasingly focused on sustainable energy solutions, solid oxide fuel cells (SOFCs) are emerging as a promising technology. Imagine a device that converts chemical energy into electrical energy with high efficiency and the ability to run on various fuels. That’s the promise of SOFCs. However, significant hurdles remain before SOFCs can become a mainstream energy source.
One of the major challenges is the high operating temperatures required by traditional SOFCs, typically between 800 and 1000°C. These high temperatures lead to increased costs and reduced reliability, hindering their widespread adoption. To combat this, researchers have been developing intermediate-temperature SOFCs (IT-SOFCs) that operate between 500 and 800°C. A key component in these IT-SOFCs is the cathode material, with lanthanum strontium cobalt ferrite (LSCF) being a popular choice due to its enhanced performance at lower temperatures.
A recent study has shed light on how the addition of cobalt oxide (Co3O4) during the sintering process can significantly impact the performance of LSCF-based cathodes. Sintering, a heat treatment process used to bond particles together, is crucial in determining the final microstructure and performance of the cathode. The study focuses on how different concentrations of Co3O4 affect the ohmic transport and electrode performance of LSCF-gadolinia-doped ceria (LSCF-GDC) cathodes, providing valuable insights into optimizing SOFC design.
The Cobalt Advantage: Optimizing SOFC Performance
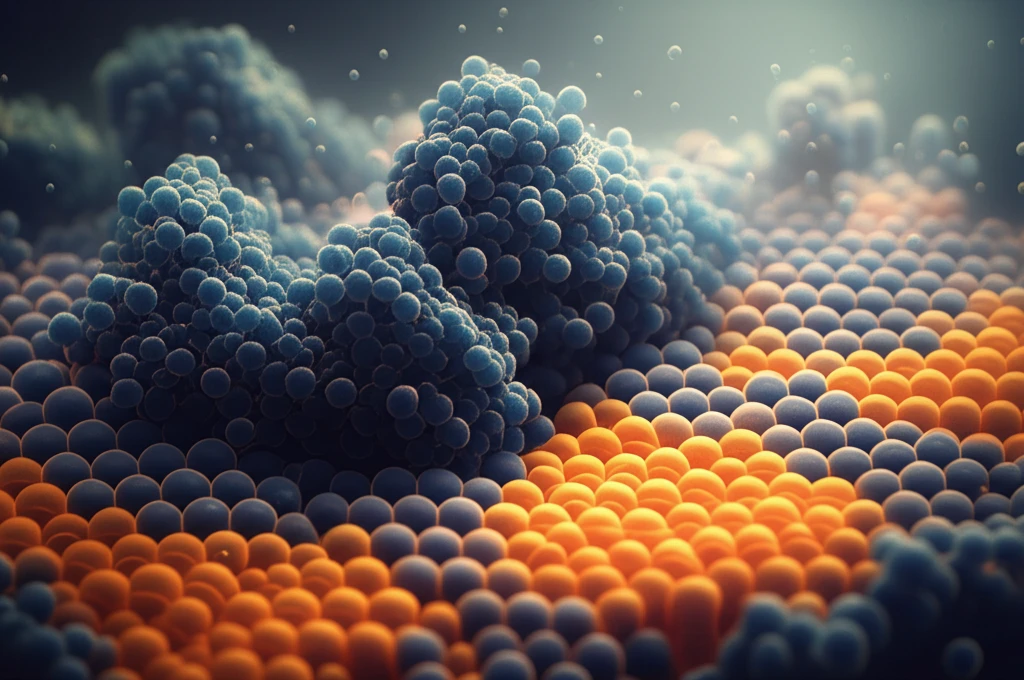
The research reveals a strong correlation between the concentration of Co3O4 and the performance of the LSCF-GDC cathodes. The most effective performance was achieved with a Co3O4 concentration between 4 and 5 wt%. This optimal range leads to smaller grain sizes and improved connections between particles, which are essential for efficient electron transport. This discovery suggests that carefully controlling the amount of Co3O4 can significantly enhance the electrochemical activity of the cathode.
- Optimal Concentration: Best results with 4-5 wt% Co3O4.
- Grain Size: Smaller grain sizes improve performance.
- Charge Transfer: Co3O4 boosts charge transfer in the LSCF-GDC layer.
- Electronic Transport: Moderate impact in the LSCF layer.
Future Implications and Next Steps
This research provides valuable insights into optimizing the performance of LSCF-based cathodes through the strategic use of Co3O4. By carefully controlling the concentration of Co3O4 and managing the sintering process, it’s possible to create more efficient and cost-effective SOFCs. These advancements bring us closer to a future where clean energy is more accessible and sustainable. Further research is needed to explore the long-term effects of Co3O4 addition and to develop strategies for mitigating thermal stress. These efforts will pave the way for the widespread adoption of SOFC technology.