Declutter Your Way to Success: How 5S Implementation Can Transform Your Workspace
"Unlock hidden potential and boost productivity: A practical guide to implementing the 5S methodology in your manufacturing facility and beyond."
In today's fast-paced and competitive business environment, manufacturers face constant pressure to improve efficiency, reduce waste, and enhance product quality. Customers demand high standards, and organizations must optimize their operations to meet these expectations. The 5S methodology offers a simple yet powerful framework for achieving these goals.
The 5S system focuses on creating a clean, organized, and efficient workspace, eliminating waste and optimizing productivity. By systematically addressing workplace organization, 5S can lead to significant improvements in various aspects of a manufacturing operation, from increased output to enhanced safety.
This article explores the core principles of 5S implementation, offering practical guidance on how to apply these techniques in your manufacturing facility. We’ll delve into real-world examples of companies that have successfully transformed their operations using 5S, and provide a step-by-step approach to implementing this methodology for lasting results.
Understanding the 5S Methodology: A Foundation for Workplace Excellence
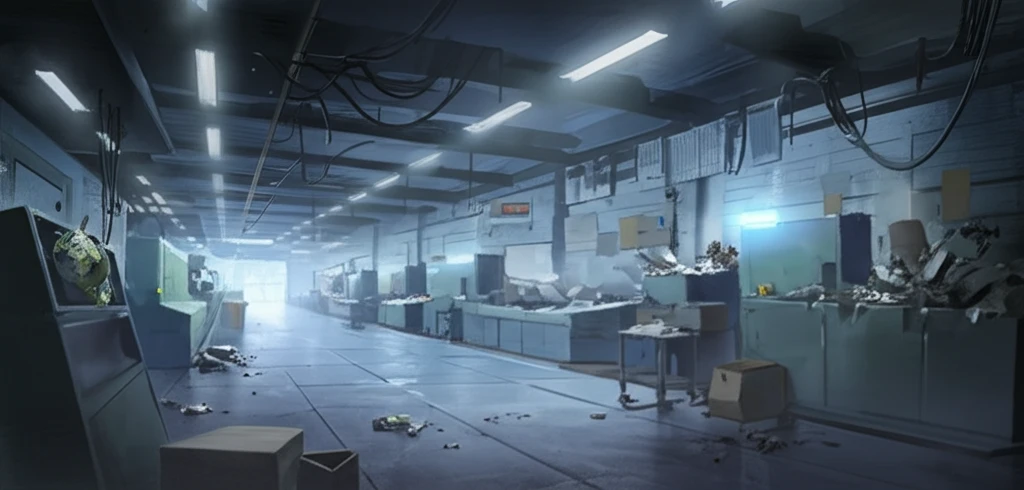
The 5S methodology is a structured approach to workplace organization and standardization, originating in Japan and widely adopted across various industries. The five pillars of 5S are:
- Sort (Seiri): Eliminate unnecessary items from the workspace, keeping only essential tools and materials. This involves identifying and removing clutter, reducing hazards, and freeing up valuable space.
- Set in Order (Seiton): Arrange the remaining items in a logical and accessible manner, ensuring that everything has a designated place. This promotes efficiency and reduces wasted time searching for tools or materials.
- Shine (Seiso): Clean the workspace thoroughly and regularly, maintaining a spotless environment. This not only improves aesthetics but also helps identify potential equipment malfunctions or safety hazards.
- Standardize (Seiketsu): Establish procedures and standards to maintain the sorted, organized, and clean workspace. This ensures consistency and prevents the workplace from reverting to its previous state.
- Sustain (Shitsuke): Develop a culture of continuous improvement, encouraging employees to adhere to the 5S principles and actively participate in maintaining the workplace standards. This requires ongoing training, communication, and recognition.
Transform Your Manufacturing Facility with 5S Today
Implementing the 5S methodology can be a transformative journey for any manufacturing facility. By following the steps outlined in this article and adapting them to your specific needs, you can create a more efficient, safer, and more productive workplace. Embrace the power of 5S and unlock the hidden potential within your organization.