Crane Control Revolution: How Smart Algorithms are Preventing Accidents
"Discover how Dynamic Differential Evolution algorithms are optimizing sliding mode controllers to make under-actuated cranes safer and more efficient."
Cranes are the unsung heroes of construction sites, harbors, and industrial factories, tirelessly lifting and moving heavy loads. Under-actuated cranes, known for their wide application in heavy cargo transportation, present unique challenges. Unlike fully-actuated systems, these cranes have fewer control inputs than degrees of freedom, making precise control a complex task.
One of the most critical issues is payload oscillation. The high-speed movement of the trolley can easily cause the payload to swing, leading to potential collisions and safety hazards. As such, designing effective anti-swing controllers is paramount.
The need for innovation in crane control is driving research toward smarter, more adaptive systems. In a groundbreaking study published in IEEE Access in September 2018, researchers Zhe Sun, Xuejian Zhao, Zhixin Sun, Feng Xiang, and Chunjing Mao introduced an optimal sliding mode controller design based on a Dynamic Differential Evolutionary (DDE) algorithm for under-actuated crane systems.
The Innovative DDE-SMC Solution
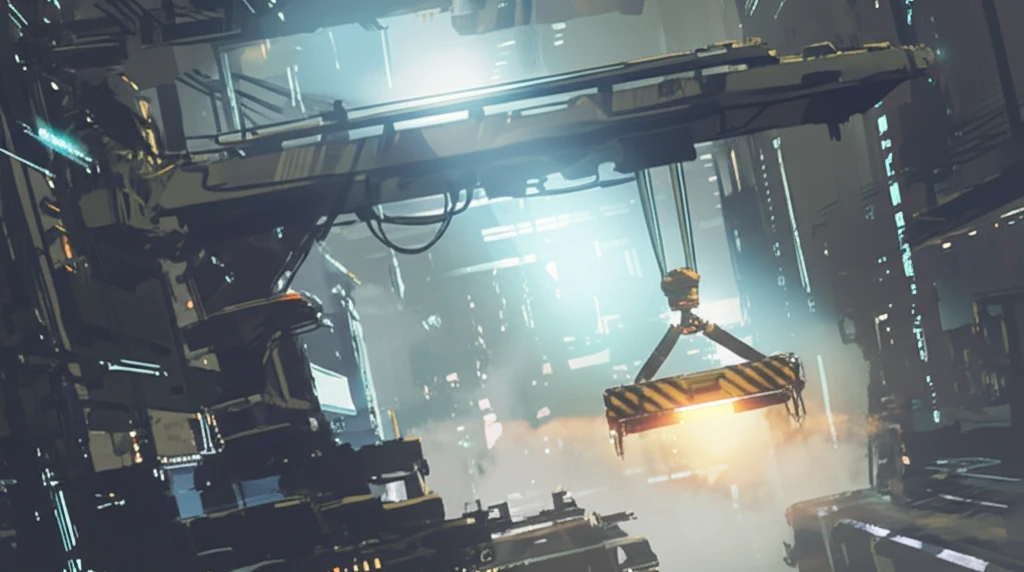
The core of this innovation lies in the Dynamic Differential Evolution algorithm-based sliding-mode controller (DDE-SMC). This method aims to tackle the residual vibration problem in under-actuated crane systems with a novel approach.
- Fusion Sliding Function: Combines position and angle sliding functions to provide a comprehensive control strategy.
- Switching and Equivalent Control Law: Designed to ensure precise control throughout the lifting process.
- Dynamic Differential Evolution (DDE) Algorithm: Optimizes control parameters to enhance anti-swing performance.
Future of Crane Systems
The potential of DDE-SMC extends beyond just reducing accidents. By improving the efficiency and precision of crane operations, industries can see increased productivity, reduced material waste, and safer working conditions. As AI and machine learning continue to evolve, expect even more sophisticated solutions that make workplaces safer and more efficient.