Brass Under Pressure: Unlocking the Secrets to Stronger, Longer-Lasting Metals
"Discover how laser shock peening (LSP) can revolutionize the fatigue resistance of brass and other metal alloys, leading to safer and more durable products."
In today's world, the demand for robust and reliable metal components is ever-increasing. From the springs in your car to the bearings in heavy machinery, metal alloys are the unsung heroes of countless applications. However, these components often face a relentless enemy: fatigue. Fatigue, the weakening of a material due to repeated stress, is a leading cause of failure in metallic structures. Understanding and mitigating fatigue is therefore crucial for ensuring the safety, longevity, and efficiency of countless products.
Copper alloys, prized for their excellent workability and fatigue resistance, are frequently used in critical applications. Yet, even these materials are susceptible to fatigue failure under cyclic loading. Enter laser shock peening (LSP), a revolutionary surface modification technology that's changing the game for metal durability. LSP can dramatically improve the fatigue resistance of materials by inducing compressive residual stress and modifying the material's microstructure.
Imagine a world where bridges last longer, airplanes fly safer, and machinery operates more reliably – all thanks to a deeper understanding of how to strengthen metals at a microscopic level. This is the promise of LSP, and researchers are working tirelessly to unlock its full potential. Let's delve into the science behind LSP, exploring how it works, its benefits, and its transformative impact on the world of metal alloys.
The Science of Laser Shock Peening: Transforming Metal from the Inside Out
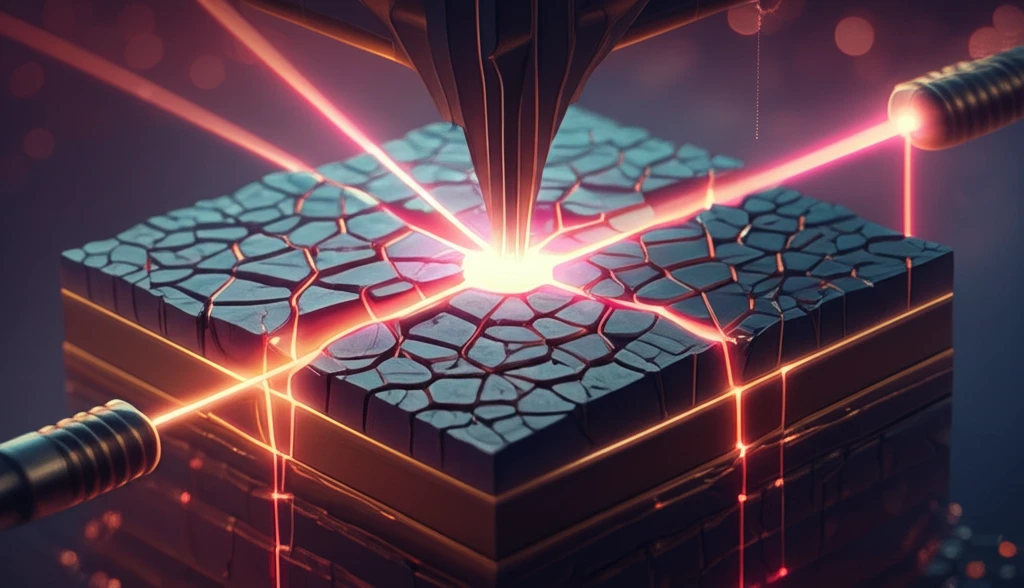
Laser shock peening (LSP) is a sophisticated process that uses high-energy laser pulses to create shockwaves on the surface of a metal. This process isn't just skin-deep; it alters the very microstructure of the material, leading to significant improvements in its resistance to fatigue and other forms of stress. It works by using focused bursts of high-energy laser light to create plasma on the surface of the material. This plasma rapidly expands, generating a powerful shockwave that propagates through the metal.
- Increases compressive residual stress: Making the metal more resistant to cracking.
- Refines grain structure: Enhancing strength and toughness.
- Extends fatigue life: Allowing metal components to last longer under stress.
- Transfers fatigue crack initiation from surface to subsurface.
The Future of Metals: Stronger, Safer, and More Sustainable
Laser shock peening represents a paradigm shift in how we approach metal durability. By understanding and harnessing the power of LSP, engineers and scientists can create materials that are stronger, safer, and more sustainable. As research continues, we can expect to see even more innovative applications of LSP across diverse industries, from aerospace and automotive to medical devices and infrastructure.