Boosting Business Performance: How Six Sigma and System Dynamics Work Together
"Discover how integrating Six Sigma's data-driven process with System Dynamics' holistic modeling can transform your manufacturing systems and drive continuous improvement."
In today's competitive landscape, manufacturing companies need every edge they can get. They're constantly seeking tools and methodologies that not only support decision-making but also drive tangible improvements in processes. Industrial systems are inherently complex, and managing them effectively requires understanding the dynamic behaviors at play. This is where continuous improvement comes in – a proactive, ongoing effort to enhance products and services. Learning is at the heart of this process, enabling teams to generate innovative ideas, test solutions, and implement lasting change.
One potent tool for achieving continuous improvement is Six Sigma, a data-driven methodology focused on minimizing defects and maximizing efficiency. Introduced by Motorola in 1987, Six Sigma provides a structured approach to process upgrading and new product development, relying on statistical and scientific methods to achieve dramatic reductions in customer-defined defect rates.
At the same time, System Dynamics offers a complementary approach by providing a way to understand and manage the complex interactions within a system. By creating computer simulation models, System Dynamics captures the causal interlinks and feedback loops that drive system behavior. Integrating System Dynamics with Six Sigma's DMAIC (Define, Measure, Analyze, Improve, Control) methodology can provide a powerful framework for understanding and improving manufacturing processes.
Unlocking Synergies: How Six Sigma and System Dynamics Work Together
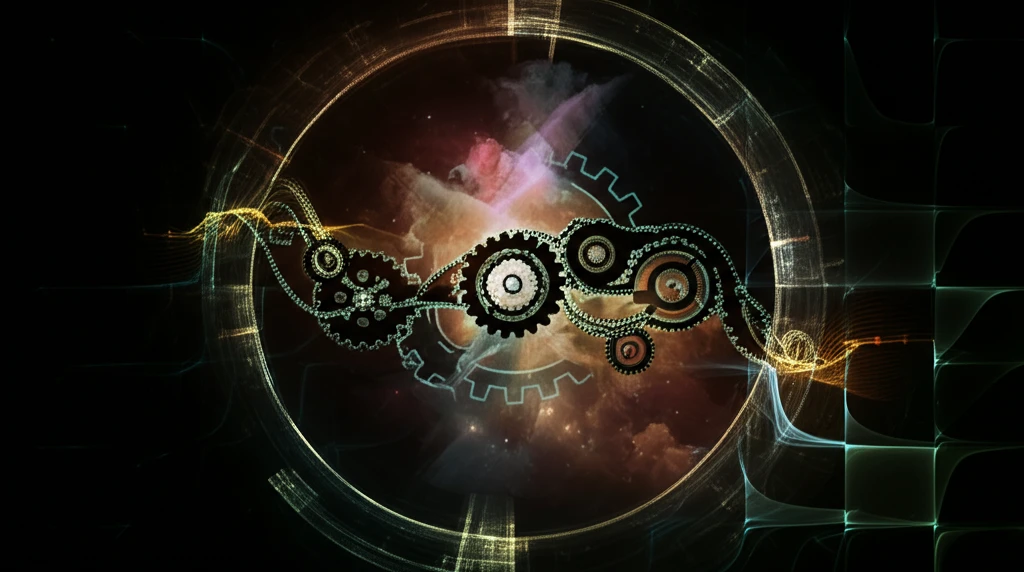
Six Sigma employs the DMAIC methodology to drive dramatic improvements. This involves Define, Measure, Analyze, Improve, and Control. The goal is to establish a baseline, measure process effectiveness, analyze data to identify root causes, implement improvements, and monitor the changes to sustain gains. However, manufacturing systems aren't isolated; they consist of dependent events and variations, requiring a systems approach.
- Define: Articulate the problem, collect data, select key variables, and represent them in a mental map to build a dynamic hypothesis.
- Measure: Formulate a model, develop equations, and create a Forrester diagram to carry out simulations.
- Analyze: Study the simulation results to understand system behavior and identify areas for improvement.
- Improve: Validate the model through sensitivity analysis to ensure its robustness and identify optimal solutions.
- Control: Propose operation policies and monitoring techniques to sustain the improvements achieved.
The Road Ahead: Building a Culture of Continuous Improvement
The integration of Six Sigma and System Dynamics offers a promising path toward enhancing manufacturing performance. By embracing this holistic approach, companies can not only solve immediate problems but also build a culture of continuous improvement, driving sustained success and competitive advantage in the long run. As future work, consider expanding the application of system dynamics to the entire supply chain, further optimizing performance and resilience.