Aluminum 3D Printing Breakthrough: Eradicating Defects for Perfect Products
"New research unveils the secrets to eliminating hole-defects in aluminum droplet printing, paving the way for stronger, smoother, and more reliable 3D-printed metal parts."
3D printing is revolutionizing manufacturing, offering the ability to create complex shapes and customized parts with unprecedented ease. Among the various materials used in 3D printing, aluminum stands out due to its lightweight nature, strength, and corrosion resistance. However, achieving consistently high-quality aluminum 3D prints has been a challenge, especially when it comes to creating parts with smooth inner surfaces. This is a hurdle, especially in industries that demand precision and reliability.
One major obstacle in aluminum 3D printing is the formation of tiny imperfections called 'hole-defects'. These defects, which appear as voids or gaps on the inner surfaces of printed parts, can compromise the strength, durability, and overall performance of the final product. Imagine creating a complex component for an aerospace application, only to find that it's riddled with microscopic flaws that could lead to failure. That is what researchers are trying to avoid.
Fortunately, a team of researchers from Northwestern Polytechnical University and California State University has made a significant breakthrough in understanding and eliminating these hole-defects. Their innovative approach, which involves using soluble cores and carefully controlling the droplet printing process, promises to pave the way for consistently flawless aluminum 3D prints.
The Science Behind Hole-Defects: Understanding the Problem
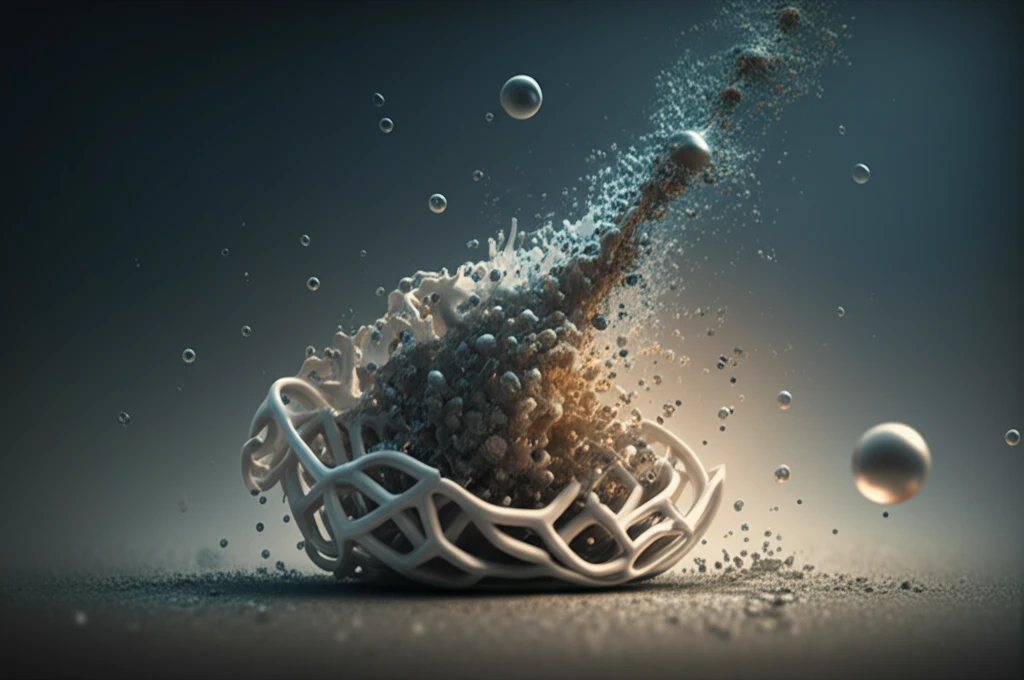
Before we dive into the solution, let's take a closer look at how these hole-defects form in the first place. The researchers pinpointed the primary cause as the incomplete fusion of molten aluminum droplets during the printing process. Imagine tiny droplets of molten metal being deposited layer by layer to build a 3D structure. If these droplets don't fully merge and bond together, gaps and voids can appear on the inner surfaces of the printed part. It is the gaps and voids that become hole-defects.
- Droplet Temperature: If the aluminum droplets aren't hot enough, they may solidify too quickly, preventing them from fully merging with neighboring droplets.
- Substrate Temperature: The temperature of the surface onto which the droplets are deposited also plays a crucial role. If the substrate is too cold, it can cause the droplets to cool too rapidly, hindering fusion.
- Surface Tension: The surface tension of the molten aluminum can also affect how well the droplets spread and merge together.
- Printing Parameters: The speed and pattern of droplet deposition can also influence the formation of hole-defects.
The Future of Aluminum 3D Printing: Stronger, Smoother, and More Reliable Parts
The research by Yi, Qi, Luo, and Li represents a significant step forward in aluminum 3D printing. By understanding the mechanisms behind hole-defect formation and developing strategies to eliminate them, they've paved the way for creating stronger, smoother, and more reliable 3D-printed aluminum parts. This breakthrough has the potential to unlock new applications for aluminum 3D printing in industries ranging from aerospace and automotive to medical devices and consumer electronics. As 3D printing technology continues to evolve, we can expect even more innovations that push the boundaries of what's possible.