Unlocking Cleaner Fluorite: How a Novel Method Could Revolutionize Industrial Production
"A new approach to purifying fluorite concentrate promises safer, more efficient processes and higher quality materials for a range of industries."
Fluorite, a mineral rich in fluoride, is a critical raw material in numerous industrial applications. China, as the world's leading producer of fluorite concentrate, plays a pivotal role in its global supply. However, raw fluorite often comes with unwanted companions: sulfide and calcite minerals.
The presence of these 'impurities' can cause significant headaches in industries that rely on fluorite, particularly in the production of anhydrous hydrofluoric acid (AHF). Sulfides and calcites can lead to pipe blockages, reduce efficiency, and even pose safety risks. This is where innovation steps in.
Traditional methods of fluorite purification, such as direct flotation, struggle to effectively separate fluorite from these troublesome minerals due to their similar behaviors. But now, a novel method combining acid leaching and reverse flotation has emerged, promising a more effective and cleaner way to refine fluorite concentrate.
The Power of Two: Acid Leaching and Reverse Flotation
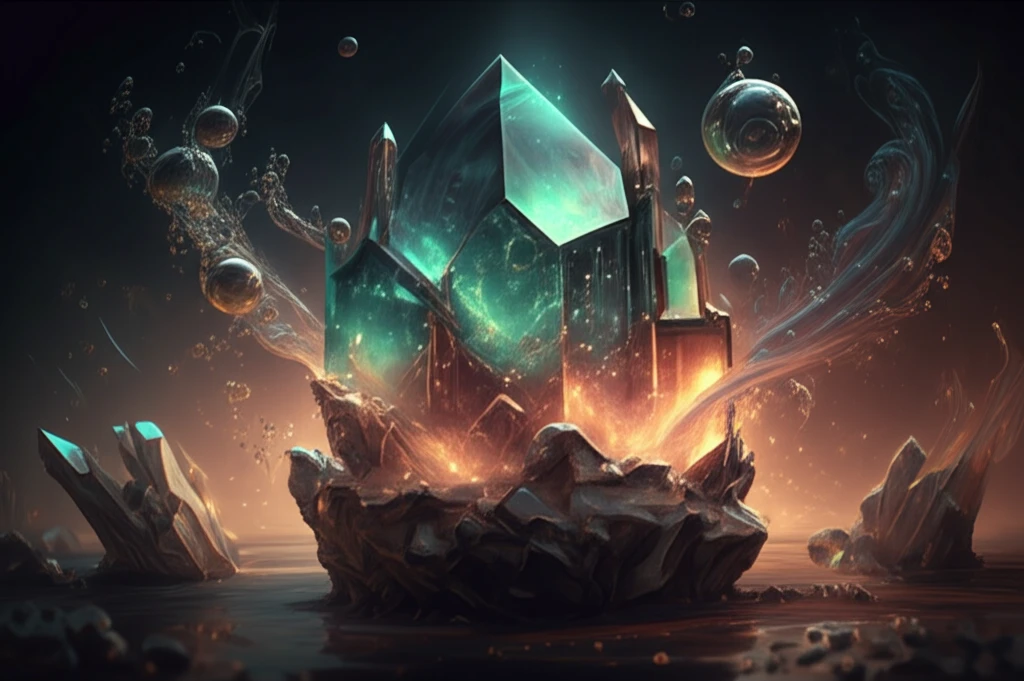
The core of this innovative method lies in its two-pronged approach. First, acid leaching uses hydrochloric acid to dissolve calcite. This process not only removes a problematic impurity but also undermines the effectiveness of fatty acids, which are commonly used as collectors in traditional flotation methods.
- Acid Leaching: Hydrochloric acid dissolves calcite, neutralizing the activity of fatty acids.
- Reverse Flotation: Butyl xanthate selectively collects sulfides, which are then separated using terpenic oil as a foaming agent.
A Greener, Safer, and More Profitable Future for Fluorite
This innovative approach to fluorite purification not only promises higher quality materials but also contributes to safer and more sustainable industrial practices. By reducing pipe blockages, minimizing waste, and enhancing the efficiency of AHF production, this method paves the way for a greener, safer, and more profitable future for the fluorite industry.