Metal Powders: The Unsung Heroes of 3D Printing's Future
"Unlock the potential of additive manufacturing with the right metal powder: A deep dive into characterization, recycling, and why it all matters for the future of 3D-printed parts."
Additive manufacturing (AM), or 3D printing, is transforming how we create metal parts. Unlike traditional methods that carve away material, AM builds parts layer by layer, opening doors to complex designs and customized solutions, especially for critical components in aerospace and beyond. But creating AM parts with consistent, reliable properties hinges on one key factor: the metal powders used as input materials.
Think of metal powders as the ink for a 3D printer – if the ink is inconsistent, the final print will suffer. This means understanding and controlling the characteristics of these powders is crucial. Standardized measurement methods are needed to ensure every batch meets the required specifications, leading to predictable part performance.
This article explores the world of metal powders in AM, drawing insights from research conducted at the National Institute of Standards and Technology (NIST). We'll delve into how existing methods are used, the impact of recycling on powder properties, and the cutting-edge techniques used to unlock the secrets hidden within these tiny metallic particles.
Why Powder Characterization is the Key to Unlocking AM's Potential
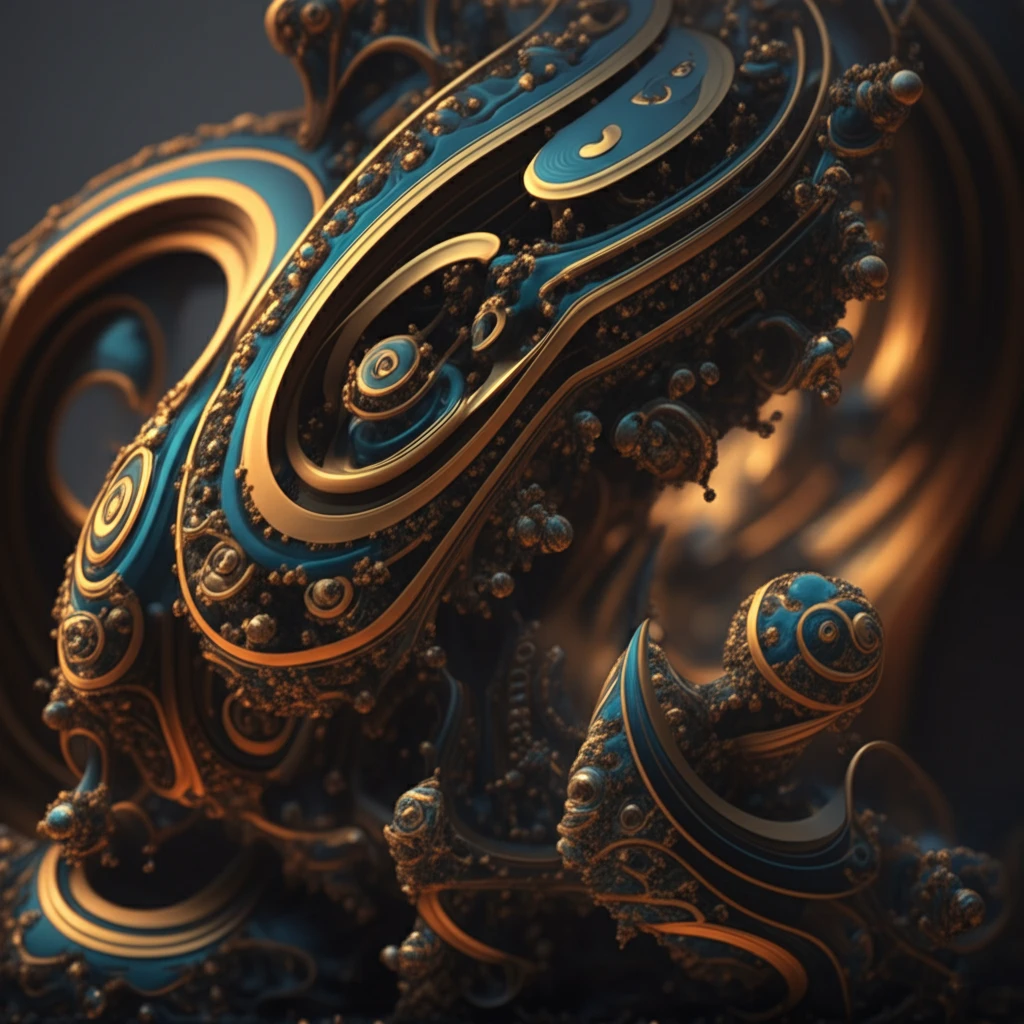
Imagine trying to bake a cake without measuring your ingredients. The result would likely be a disaster! Similarly, in AM, inconsistent powder characteristics can lead to parts with defects, varying densities, and unreliable mechanical properties. Characterizing metal powders is about gathering data that allows engineers to predict how the powder will behave during the AM process, and, ultimately, how the finished part will perform.
- Particle Size Distribution: Ensuring the powder contains the right mix of particle sizes for optimal packing and flow.
- Particle Shape: Spherical particles generally lead to better flow and more consistent packing, influencing part density.
- Density: Knowing the true density of the powder is essential for calculating the porosity of the final part.
- Chemical Composition: Ensuring the powder has the correct elemental makeup and that surface oxidation is controlled.
- Flowability: How easily the powder flows and spreads is critical for consistent layer deposition.
The Road Ahead: Standardizing Powder Characterization for AM's Continued Growth
The future of AM hinges on consistent, reliable metal powders. As this technology evolves, standardized measurement techniques and a deeper understanding of powder behavior will be essential. By embracing these advancements, we can unlock the full potential of additive manufacturing, creating stronger, more customized, and innovative products across industries.